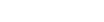
- Compresores.
Una herramienta indispensable en el taller de chapa y pintura es el compresor.
Compresores - Definición: Son máquinas que aspiran aire ambiente a la
presión y temperatura atmosférica y
lo comprime hasta conferirle una presión superior.
Son las máquinas generadoras de aire comprimido.
Existen varios tipos de compresores, dependiendo la
elección de las necesidades y características
de utilización.
Compresores a pistón: Son los de uso mas difundido, en donde la compresión
se efectúa por el movimiento alternativo de
un pistón accionado por un mecanismo biela-manivela.
En la carrera descendente se abre la válvula
de admisión automática y el cilindro
se llena de aire para luego en la carrera ascendente
comprimirlo, saliendo así por la válvula
de descarga. Una simple etapa de compresión
como la descrita no permitirá obtener presiones
elevadas, para ello será necesario recurrir
a dos mas etapas de compresión, en donde el
aire comprimido a baja presión de una primera
etapa (3 a 4 bar) llamada de baja, es vuelto a comprimir
en otro cilindro en una segunda etapa llamada de alta,
hasta la presión final de utilización.
Puesto que la compresión produce una cierta
cantidad de calor, será necesario refrigerar
el aire entre las etapas para obtener una temperatura
final de compresión más baja.
Siguiente - Información sobre los compresores - Continuación > Compresores a tornillo, etc..
|