También llamados compresores helicoidales.
La compresión de estas maquinas es efectuada
por dos rotores helicoidales, uno macho y otro hembra
que son prácticamente dos tornillos engranados
entre sí y contenidos en una carcasa dentro
de la cual giran.
El macho es un tornillo de 4 entradas y la hembra
de 6. El macho cumple prácticamente la misma
función que el pistón en el compresor
en el compresor alternativo y la hembra la del cilindro.
En su rotación los lóbulos del macho
se introducen en los huecos de la hembra desplazando
el aire axialmente, disminuyendo su volumen y por
consiguiente aumentando su presión. Los lóbulos
se “llenan” de aire por un lado y descargan
por el otro en sentido axial.
Los dos rotores no están en contacto entre
sí, de modo tal que tanto el desgaste como
la lubricación resultan mínimos. Esto
se logra a través de un juego de engranajes
que mantiene el sincronismo de giro de los rotores
y evita que estos presionen unos contra otros, asegurándose
la estanqueidad necesaria por la estrecha tolerancia
de los juegos que existen entre ellos y la de estos
con la carcasa.
Se construyen de 1, 2 o más escalones
de compresión y entregan un flujo casi continuo
por lo que las dimensiones del deposito son reducidas,
cumpliendo mas bien funciones de colector y separador
de aceite que de acumulador.
El campo de aplicación de estos va desde 600
a 40.000 m /h y se logran presiones de hasta 25 bar
Ejemplos sobre el mismo depósito, con secador
frigorífico y de pie:
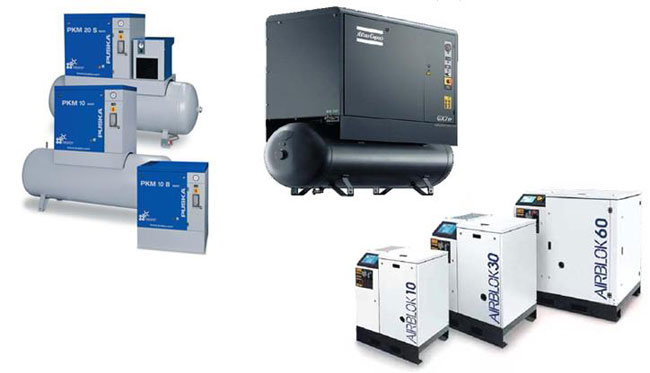
Compresores a membrana:
Son de construcción sencilla y consisten en
una membrana accionada por una biela montada sobre
un eje motor excéntrico; de este modo se obtendrá
un movimiento de vaivén de la membrana con
la consiguiente variación de volumen de la
cámara de compresión en donde se encuentran
alojadas las válvulas de admisión y
descarga, accionadas automáticamente por la
acción del aire.
Permiten la producción de aire comprimido absolutamente
exento de aceite, puesto que el mismo no entra en
contacto con el mecanismo de accionamiento, y en consecuencia
el aire presenta gran pureza.
Utilizados e medicina y ciertos procesos químicos
donde se requiera aire sin vestigios de aceite y de
gran pureza. No utilizados en general para uso industrial.
Ejemplos de membrana simples:
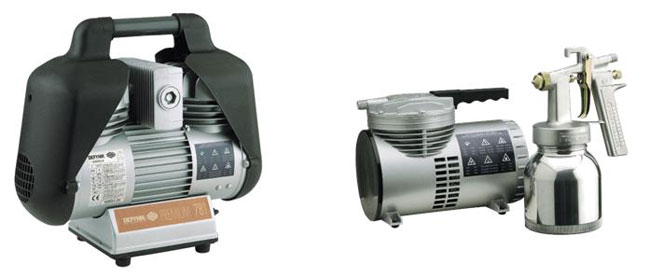
Ejemplo de
membrana silencioso:
|
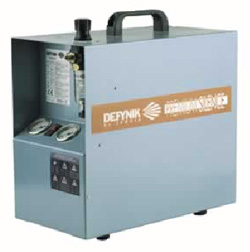 |
|
|
Compresores
a paletas:
También llamados multialetas o de émbolos
rotativos. Constan de una carcasa cilíndrica
en cuyo interior va un rotor montado un excéntricamente
de modo de rozar casi por un lado la pared de la carcasa
formando así del lado opuesto una cámara
de trabajo en forma de media luna. Esta cámara
queda dividida en secciones por un conjunto de paletas
deslizantes alojadas en ranuras radiales del rotor.
Al girar este ultimo, el volumen de las secciones
varía desde un máximo a un mínimo,
produciéndose la aspiración, compresión
y expulsión del aire sin necesidad de válvula
alguna. Este tipo de compresor es muy adecuado para
casos en que no es problema la presencia de aceite
en el aire comprimido, fabricándose unidades
de hasta 6.000 m /h de capacidad y hasta presión
de 8 bar en una sola etapa y de 30 bar en dos etapas
De requerirse aire exento de aceite, las paletas deben
ser hechas de materiales autolubricantes, tipo teflón
o grafito. Alcanzan una vida útil de 35.000
a 40.000 horas de funcionamiento dado el escaso desgaste
de los órganos móviles (paletas) por
la abundante presencia de aceite. Este tipo de compresores
suministran un flujo casi sin pulsaciones y en forma
continua utilizando un deposito de dimensiones reducida
que actúa de separador de aceite.

Compresores Roots:
Solo transportan el volumen de aire aspirado del lado
de aspiración al de compresión, sin
comprimirlo en este recorrido. No hay reducción
de volumen y por lo tanto tampoco aumento de presión.
El volumen que llega a la boca de descarga, todavía
con la presión de aspiración, se mezcla
con el aire ya comprimido de la tubería de
descarga y se introduce en la cámara llegando
este a la presión máxima siendo luego
expulsado.
Un juego de engranajes accionan los rotores en forma
sincrónica y evita que se rocen entre sí.
Resultan apropiados cuando se requiera aire comprimido
a bajas presiones completamente libre de rastros de
lubricante.
Solo se alcanzan presiones no muy superiores a 1,5
bar y por tal razón su uso es restringido en
aplicaciones neumáticas.
Compresores axiales:
Se basan en el principio de la compresión axial
y consisten en una serie de rodetes consecutivos con
alabes que comprimen el aire. Se construyen hasta
20 etapas de compresión (20 rodetes). El campo
de aplicación de este tipo de compresor alcanza
caudales desde los 200.000 a 500.000 m /h y presiones
de 5 bar, raramente usados en neumática industrial
Siguiente
- Información sobre los compresores - Continuación
> Depósitos de aire y secadores frigorificos.
Anterior
- Compresores.
Sección
de pintura
Herramientas
del pintor
Mapa web -Índice
Subir
|