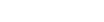
Pintura - Procesos de lijado
2.1. - Constitución y fabricación de Abrasivos - Factores que influyen
|
Factores que influyen en el acabado
Construcción: Soporte. Como se ha comentado, la dureza del soporte condiciona el acabado que se consigue. Si el soporte es más duro y rígido no se adaptará a la superficie, y será el plato el que va marcando la zona a lijar, sin embargo cuando el soporte es más flexible se va adaptando a la superficie a lijar.
Adhesivo.
Tamaño del mineral.
Disposición del mineral.
Empleo:
Velocidad.
En definitiva, no se recomienda el trabajar a velocidades muy elevadas para conseguir alargar la vida útil del producto y no provocar rugosidades demasiado elevadas.
La velocidad que se puede recomendar para cada abrasivo depende del tipo de adhesivo que componga el material. Siendo los adhesivo que usan dos capas de adhesivo sintético los que soportan mayores velocidades. La velocidad máxima de trabajo está en torno a las 8000 rpm. El rendimiento adecuado se consigue al 80% de la velocidad máxima.
Presión. El otro factor a considerar es la presión que se ejerce sobre la superficie en la que se trabaja. Existe la percepción en muchos profesionales, de que a medida que se aplica mayor presión en el plato y sobre la superficie se consigue una mayor capacidad de corte.
El factor más determinante a la hora de arrancar material es la velocidad no la presión. La aplicación de presión sólo consigue reducir la vida útil del abrasivo. No se debe aplicar mayor presión que la ejercida por el peso de la máquina y un poco más. Así se alarga la vida del abrasivo, se embaza menos el disco y la rugosidad producida es menor.
Platos. Otro de los factores clave del plato es la capacidad
de extracción de polvo que va aparejada a los platos
soportes mediante agujeros conectados con equipos
de extracción. El patrón de agujeros que muestre el
plato marcará la capacidad de extracción que llevará
a un menor embazamiento. |
|
|||
|
|